We’ve been having a minor issue with the Tesla. If you hit a bump in the road with sufficient force then the whole car goes haywire and the cruise control stops working, the regenerative braking stops working, ABS stops working – all sorts of crazy stuff. As soon as you stop the car, get out and lock it then the whole thing resets and it’s back to the normal “drive with just the accelerator” mode. So it’s not anything too worrying – just massively annoying. Massively, massively annoying. Especially annoying given the absolutely atrocious condition that British roads are in.
After combing the UK Tesla owners group posts several people were suggesting it was either a dodgy ABS sensor or a loose earth connection on the 12v battery. I checked the battery – no problem there. So I decided to jack the car up and re-seat the sensors.
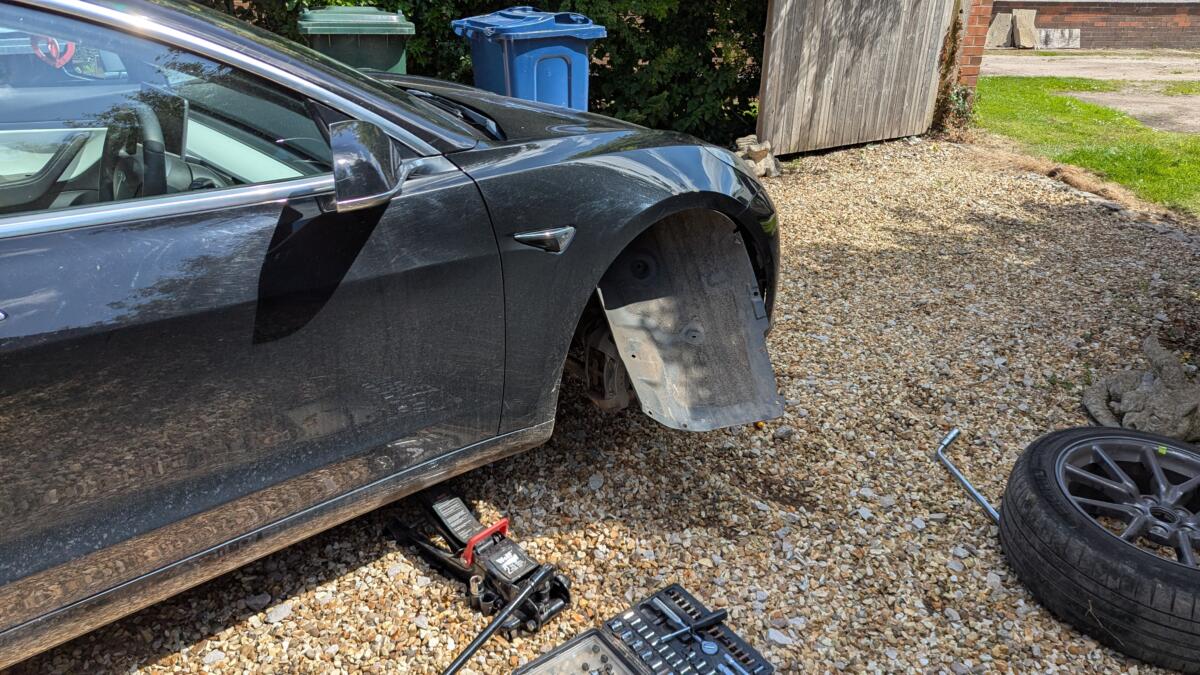
After unplugging and re-plugging the sensors I took it for a test drive. Before the work you had to hit something with quite some force to send the car mental. After the work you had to just glance in the direction of a pothole and the car would have a meltdown. I’d made it worse. Oddly though this actually encouraged me. It made me think I was messing about in the right area.
I bought a couple of new ABS sensors on eBay for £30 and then me and the boy decided to jack up the car and do the drivers side first. After doing the drivers side sensor I took it for a test drive. First bump in the road….nothing. The place where it usually goes on the drive to the high school….nothing. Speed bumps which would always trigger it…..nothing.
Pretty god damned proud of myself.